Maintenance Guide for Tool Holders
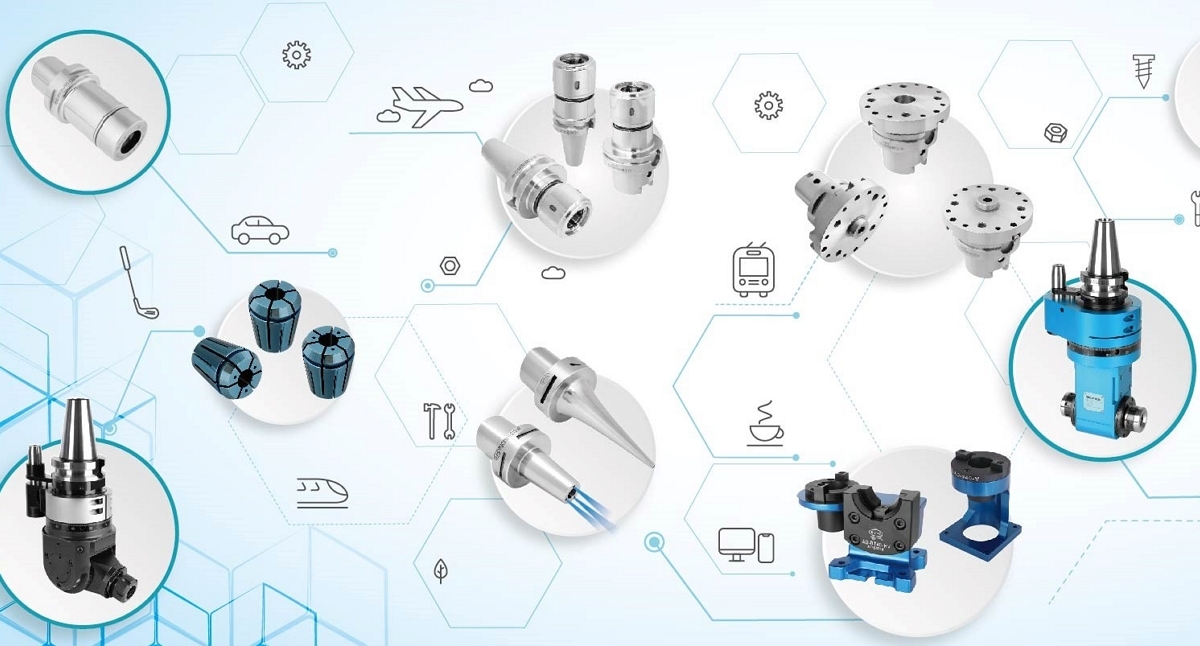
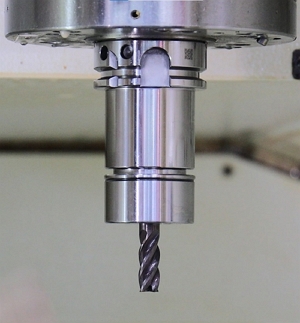
Are you experiencing rust issues with your tool holders?
During our interactions with customers, we often observe varying degrees of rust on the tool holders. In severe cases, the rusting is so extensive that even the lasered specifications become unrecognizable. Excessive rust on tool holders can directly affect their performance. For instance, rust can impact the contact between the tool holder taper and the machine spindle, leading to vibrations during machining and a shortened lifespan of the spindle. Rusting within the tool holder's inner hole may reduce the clamping force and affect the workpiece surface finish as well as the tool lifespan.
To prevent rusting of tool holders, it is recommended to perform maintenance procedures immediately after use. SYIC suggests the following maintenance steps:
STEP 1: Unload the tool holder from the spindle and use an air gun to remove metal chips and greasy dirt from the tool holder especially those in the grooves and inner hole.
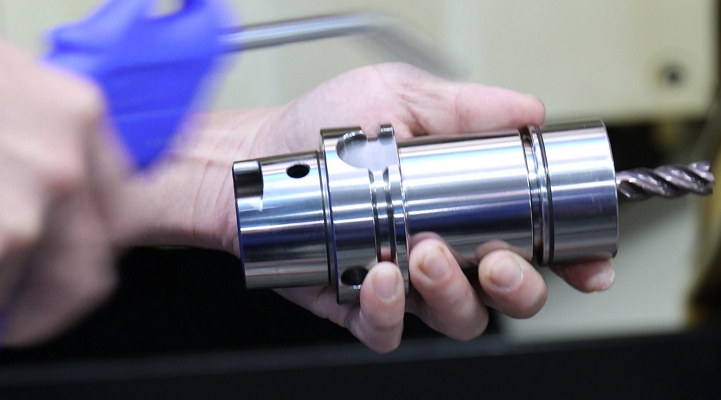
STEP 2: Use a cotton cloth or wiping paper to wipe off dirt and cutting oil from the surface. Nuts and collets should also be removed for cleaning and maintenance if applicable. If the tool holder will be left unused for a short period, it is advisable to remove the coolant supply unit and tool as well for maintenance.
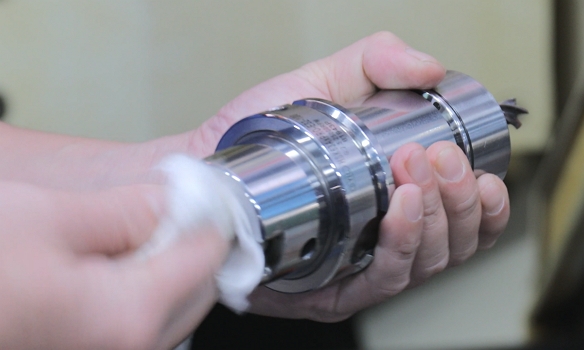
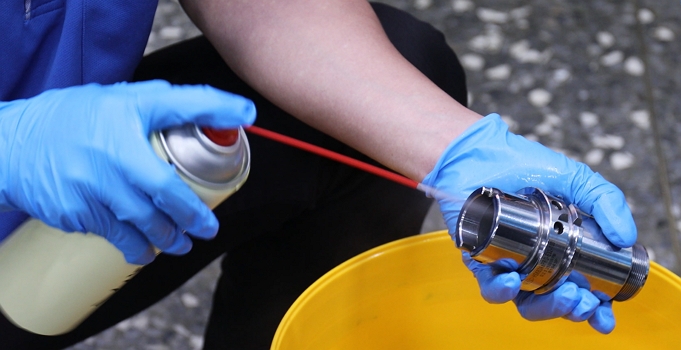
STEP 3: Wear gloves first and apply anti-rust treatment to the surface and interior of the tool holder. Wearing gloves can avoid transferring moisture or dirt residue from hands onto the tool holder, which could result in fingerprint rust stains.
STEP 4: Store the tool holder in a rustproof bag and keep it in a clean, dust-free environment.
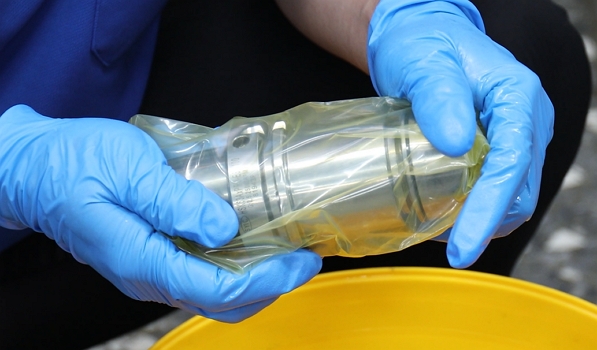
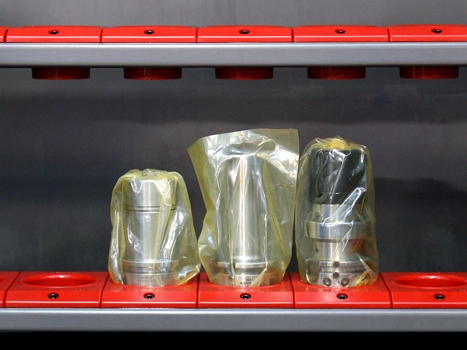
By implementing the routine of performing maintenance procedures immediately after using the tool holder, you can effectively reduce the occurrence of rust, prolong the tool holder's lifespan, and maintain machining quality. SYIC recommends adhering to these maintenance practices to ensure optimal performance and longevity of your tool holders.
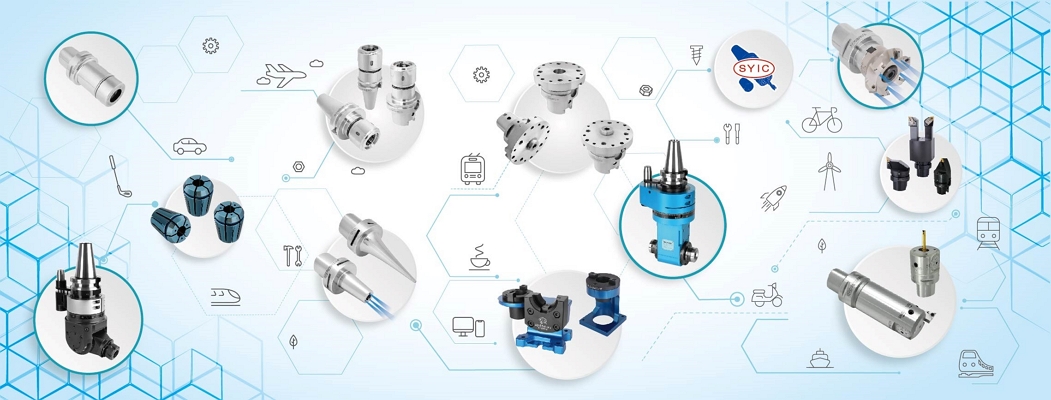