Achieving High-Precision Machining: A Guide to CNC Machine Inspection and Calibration
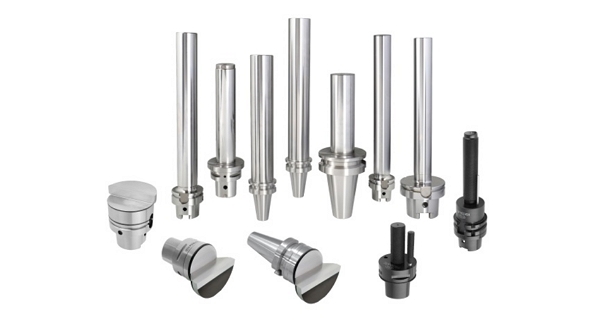
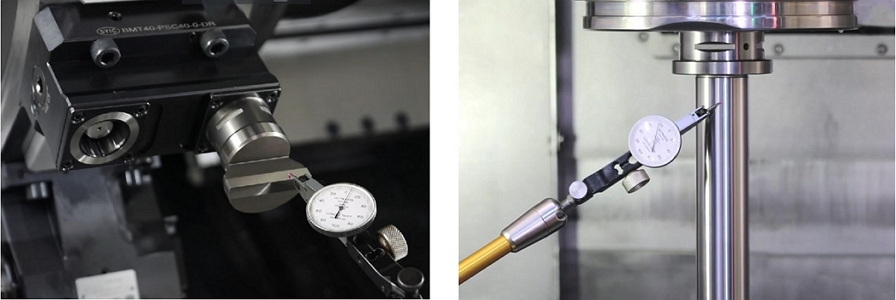
To produce a workpiece that meets quality requirements, it is essential not only to use high-performance tool holders and cutting tools on an efficient machine but also to inspect the workpiece's dimensions, accuracy, and surface roughness after machining. Besides these, what else can we do to achieve high-precision machining?
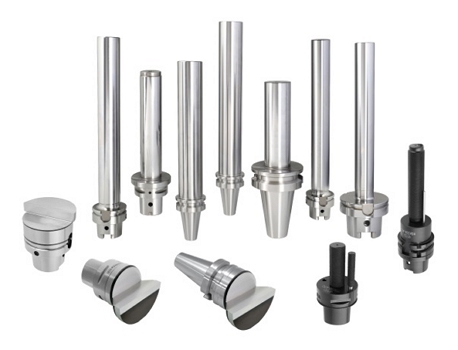
SYIC suggests “implementing regular machine inspection” is an essential step. We believe that a little precaution before a crisis occurs is preferable to a lot of fixing up afterward. Before starting production, use measuring tools for machining centers to ensure the machine accuracy is in good condition. This prevents dimensional deviations during machining, which would require more time to remedy.
SYIC offers a series of measuring tools for machining centers, such as Spindle Master Bar, which is a key tool for verifying spindle runout accuracy. It not only guarantees the machining accuracy of the workpiece but also extends the use life of the tools and spindle. In addition to the 7:24 taper like SBT and SCAT, we also provide 1:9.98 HSK hollow shank taper and 1:20 PSC polygonal structure precision spindle master bars, as well as precision turret master bars suitable for VDI and BMT mill-turn machines.
The runout accuracy of SYIC's precision spindle master bars is 3µm, and the roundness is 1µm. Each precision spindle test bar is tested with high-precision instruments and delivered with an inspection report.
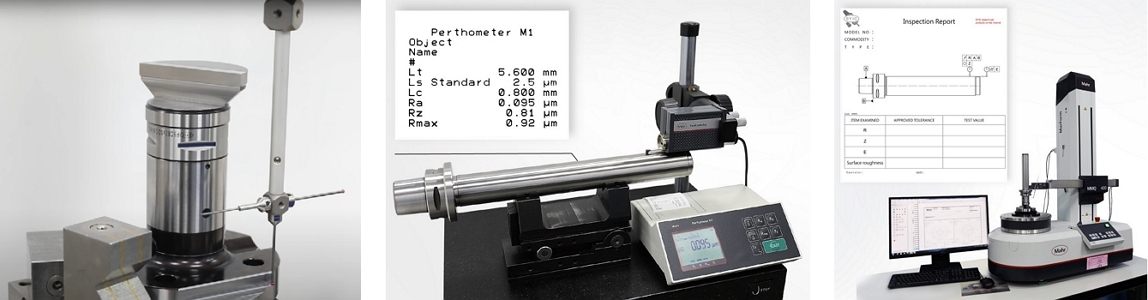
In addition to checking the spindle runout accuracy, it is also crucial to calibrate machine origin and also axial and radial accuracy of CNC machines. SYIC recommends using the SOG Origin Gauge. This product can be used to calibrate the spindle accuracy of mill-turn machines and set rotary table machining origin of 5 axis machining centers and spindle orientation (M19).
Driven by Industry 4.0, CNC machines with automatic tool change systems are now widely used in the market. They not only reduce the chance of human error but also help decrease downtime and increase production efficiency. SYIC introduces the ATC Alignment Tool Set, composed of a taper adapter, a flange adapter, and an alignment plug. It is used to check the automatic tool change positioning accuracy between the ATC arm and machine spindle, and between ATC arm and tool magazine, preventing abnormal tool holder taper wear due to tool jamming. This also helps reduce the probability of machine breakdown and extend spindle use life.
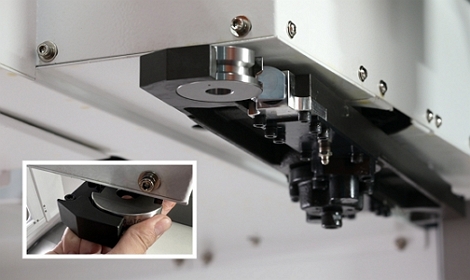
Please refer to the information of the table to choose the appropriate measuring tools for machining centers.
Function Selection | Applicable Products |
---|---|
Runout Accuracy | Spindle Master Bar 3µm BMT Turret Master Bar VDI Turret Master Bar |
Origin Accuracy | SOG Origin Gauge |
Axial and Radial Accuracy | SOG Origin Gauge |
Automatic Tool Change Positioning Accuracy between the ATC Arm and Spindle, and also Tool Magazine | ATC Alignment Tool Set |
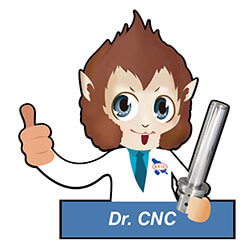
These measuring tools for machining center are like the "Dr. CNC " Health Check for CNC machines. SYIC recommends regularly using these measuring tools to check the machines, helping to identify potential issues of the machines. This saves downtime and unnecessary costs, achieving the goal of high-precision machining.
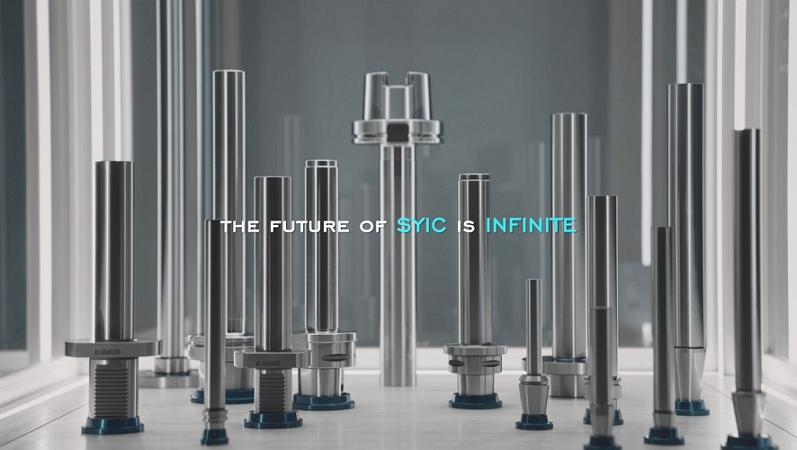