How to Choose the Right Tool Holder for Machining?
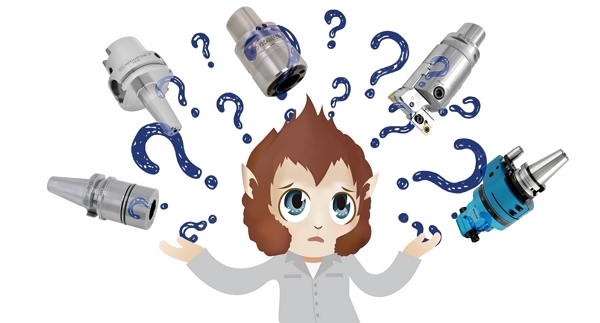
The Importance of Choosing the Right Tool Holder for Metalworking
In metalworking, tool holder is a crucial connection between the machine spindle and the cutting tool. Selecting the right tool holder can improve the production efficiency and prolong the tool use-life. It plays a significant role in controlling the quality and cost. So, how to choose the right tool holder for machining?
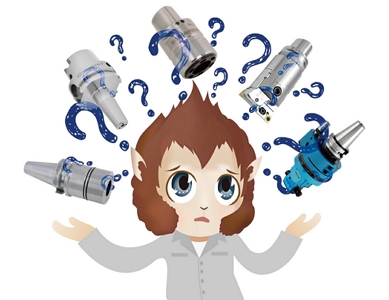
First, one must choose appropriate tool holder taper size according to the machine spindle (Please refer to SYIC’s knowledge article- Introduction of Tool Holder Tapers). Next, choose suitable tool holder clamping series based on different machining requests, such as turning, milling, drilling and boring. Furthermore, you should filter the attributes of the tool holders based on the required precision of the machined product and the machining speed of the machine. Finally, with a preliminary tool holder configuration, perform a computer simulation of the related cutting parameters before machining. This simulation helps to confirm whether there are any interference issues, verify the correctness of the selected tool holder configuration, and effectively prevent the risk of interference.
SYIC offers a variety of tool holder clamping series, including collet chucks, shrink fit holders, tapping holders, non-pull out holders, runout adjustable holders, and SDG silent damping genius holders. These tool holder clamping series are suitable for different machining needs. This article introduces the appropriate tool holder clamping series for specific machining needs to help customers achieve optimal production efficiency.
What Tool Holder is Suitable for a Five-Axis Machining Center?
For a five-axis machining center, which is geared towards curved surfaces and multi-angle machining, using a collet chuck may cause collisions with the workpiece due to the larger size of the nut. To avoid machining interference, you can choose a tool holder without a nut design. Considering the requirements for machining precision and stability, it is recommended to use a shrink fit holder. Shrink fit holder clamps the tool using the principle of thermal expansion and contraction. The tool holder is heated to expand and insert the tool, then cooled to shrink and cover the tool. This direct clamping method reduces cumulative tolerances, providing high precision and rigidity, and is suitable for high-speed machining.
SYIC's shrink fit holders offer CP coolant hole type and CUL curve line type. The former has three coolant holes at the front end to concentrate the coolant fluid on the tool for effective cooling, saving on the cost of purchasing coolant tools. CUL type is an ideal choice for five-axis machining. Its thickened neck and slim front end design provide an excellent design for avoiding interference issues but at the same time maintain machining rigidity. For five-axis machining, shrink fit holder CUL type is the best choice!
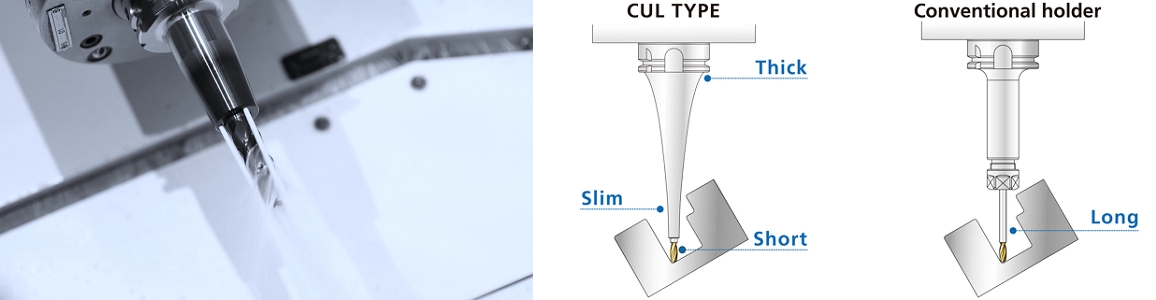
What to Do if You Don't Have a Five-Axis Machining Center but Need Side Machining?
If side machining is required on a general machine but the machine spindle or table cannot change direction due to restrictions, let the tool holder turn!
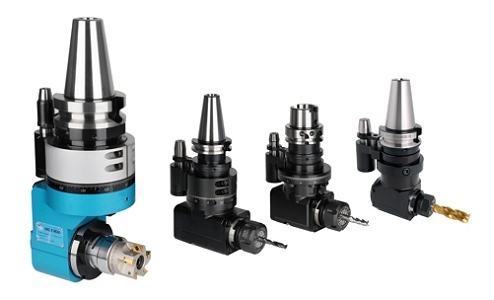
SYIC offers a series of angle heads that can change the machining direction to the spindle direction for drilling, tapping, and milling on the side of the workpiece. With the assistance of the angle head holder, you can avoid the high cost of purchasing a new machine or adding more spindles.
Besides the 90-degree angle head holders for light, medium, and heavy-duty machining, SYIC also offers the angle head holders for dual-sided machining and SAU universal angle head holder. The mandrel of SAU can be adjusted from 0 to 90 degrees, allowing you to set the angle according to the machining needs. Before use, please make sure the machine load exceeds the weight of angle head holders. After setting the large tool mode, you can operate with ATC automatic tool change, saving time on manual installation and removal of the angle head holder and improving machining efficiency.
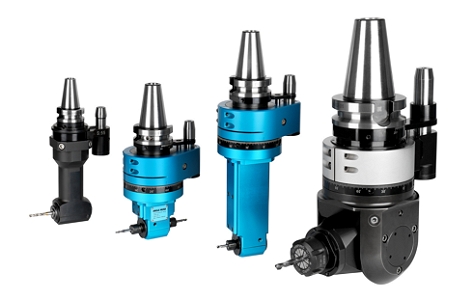
How to Improve Workpiece Machining Precision with Existing Machines?
Most metalworking shops have several older milling machines. If high workpiece precision is required, you can use SAF runout adjustable holders. These are suitable for old machines with worn spindles. By calibrating the runout accuracy with SAF runout adjustable holder before machining, you can maintain tool runout accuracy during machining, reduce tool wear, and ensure that the tool cut evenly, controlling the dimensional accuracy of the workpiece and reducing tool wear to save costs.
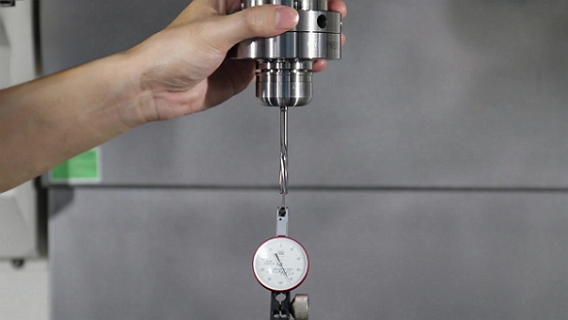
Revolutionary Upgrade Beyond ER Tool Holders
Collet chucks are the most popular when talking about CNC machining, because they allow flexible clamping diameter changes by replacing the collet. The ER system is the most widely used series. SYIC produces an ER 3.0- PRO-E precision collet chuck with an enlarged inner hole design to optimize collet coverage and reduce tool overhang length. The optimized design of PRO-E Excellent Collet Chuck also includes a two-segment straight sections locking combination at the front end of the tool holder and the thread of the nut, maximizing strength, rigidity, and precision stability. PRO-E collet chuck retains the convenience of using the entire ER series of collets.
With the innovative tool holder types mentioned above, you can eliminate the need for traditional standard tool holders and no longer rely on outdated designs. By adopting the correct machining concepts and selecting the appropriate tool holders, you can save on significant equipment or tool procurement costs, improve production efficiency, and enhance machining quality. Additionally, these tool holder series are not necessarily expensive yet can achieve new heights in machining.
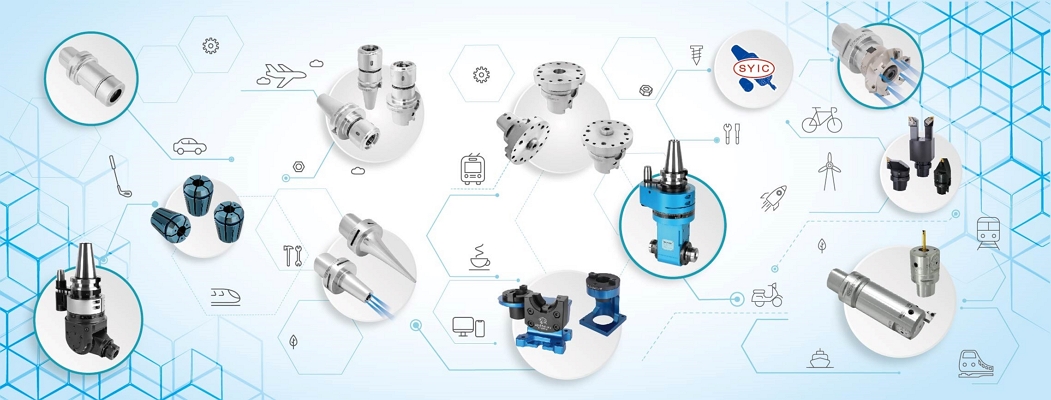