Positive Impact of High Pressure Cooling Tool Holders
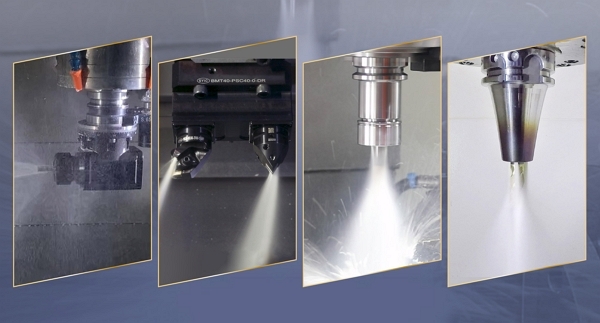
Three critical cutting factors-chip removal, heat dissipation, and effective cutting:
During the cutting process, three critical factors are chip removal, heat dissipation, and ensuring effective cutting rather than extruding. First, efficient chips removal prevents extruding of chips on the workpiece surface so it reduces tools wear and improves surface finish of workpieces. Second, cutting generates heat that makes the temperature rise on both of tools and surface of workpieces. Excessive temperature may cause the tool edge deformation and result in inaccurate workpiece dimensions. Effective heat dissipation extends tool life and enhances machining quality. Moreover, effective cutting reduces friction and pressure during machining, thereby improving efficiency and precision.
Definition & Advantages of High-Pressure Coolant System
Introduction of Coolant Pressure Levels:
Low coolant pressure | Under 7 Bar (under 100 PSI) |
It’s commonly seen in machining center. Cooling performance is poor and it cannot reduce tool wear. |
---|---|---|
Medium coolant pressure | 20 ~ 60 Bar (300 ~ 900 PSI) |
Under general machining conditions, it can effectively improve machining efficiency and extend tool life. |
High coolant pressure | 70 ~ 100 Bar (1,000 ~ 1,500 PSI) |
It achieves optimal machining efficiency, maximizes tool life, effectively processes difficult-to-cut materials and solves issues of entangled chips. |
Ultra-high coolant pressure | Over 100 Bar (over 1,500 PSI) |
It applies for machining superalloy and utmost difficult-to-cut materials. |
High-pressure coolant system is a technology that injects coolant directly onto the cutting zone under high pressure. It can effectively remove chips and dissipate the heat generated during cutting. A machining center equipped with a high-pressure coolant system can optimize cutting parameters, increase cutting speed and feed rate, improve production capacities, reduce production costs, extend tool life, and improve the surface finish of workpieces.
SYIC offers a range of high-efficiency products with built-in cooling features. The following is the application of some selected products:
1. PRO-E Excellent Collet Chuck and the Application of ER Collets
PRO-E excellent collet chucks are used with standard ER collets (ISO15488). SYIC produces a diverse range of ER collets, including ER-E-CO high precision sealed collets, ER-E-FID and ER-E-FOD coolant collets, as well as ERS metallic sealed collets, and ERS coolant collets (FID and FOD types). The runout accuracy and coolant pressure are shown in the table below.
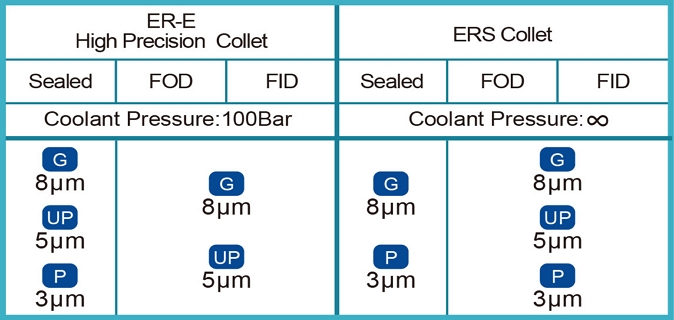
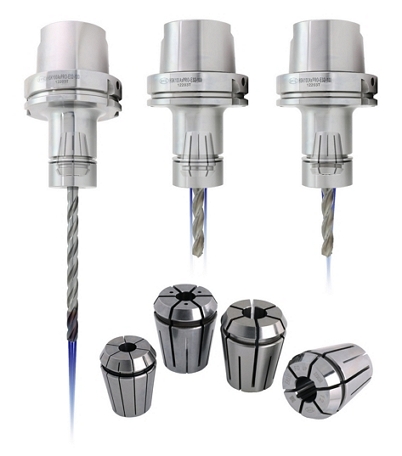
ER-E collets differ from standard ER collets by having 12 slots, which bring better accuracy stability and less influences to runout accuracy due to users’ improper clamping. For FID coolant flute type of collets, the coolant fluid outlet is through the internal grooves of the collet and goes parallel with the tool thus there is no tool effective length limit. FOD coolant hole type of collets feature three coolant holes pointing towards the center of the tool, suitable for tools with a length-to-diameter ratio of 2.7DL to 3.5DL. Customers can choose based on their specific coolant needs to perfectly achieve their machining objectives.
2. Shrink Fit Chuck with CP Coolant Hole and Shrink Fit Chuck CUD Type with CP Coolant Hole
SYIC has two series of CP type shrink fit chucks-standard type and CUD curved line type. Both have three coolant holes at the end face, focusing coolant directly on the tool for effective cooling, suitable for non-coolant through tools that saves the cost on purchasing coolant through tools. These coolant holes direct the coolant fluid to the tools, ensuring efficient chip removal and cooling, maintaining workpiece dimension stability and surface roughness.
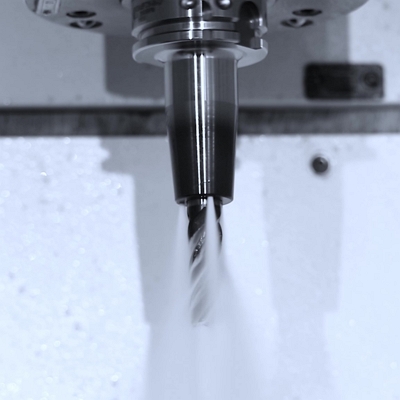
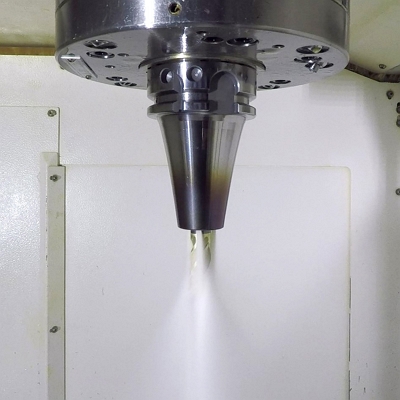
Shrink fit chuck CUD type with CP coolant hole features the design of CUL curved line to minimize machining interference. Comparing to CUL type shrink fit chuck, the front wall of the CUD-CP is thicker, providing superior machining rigidity. It is suitable for machining irregular shapes, curves, and pocket workpieces.
3. Upgraded Oil Hole Holder and Angle Head Holder
SYIC has launched upgraded "Oil Hole Holder, increasing the maximum revolution from 3,000 rpm in standard models to 5,000 rpm, and raising coolant pressure from 7 Bar to 30 Bar. The upgraded "SAM-HSC angle head holder" now supports maximum revolution 8000 rpm compared to 4,000 rpm in standard models, with coolant pressure increased from 7 Bar to 20 Bar. These enhanced designs provide better cooling effects during deep-hole machining and high-difficulty cutting operations, improving chip removal and cooling capabilities, thereby boosting machining efficiency.
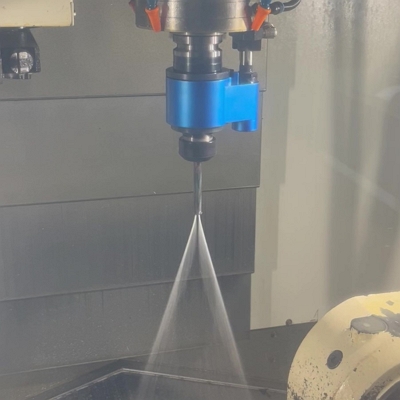
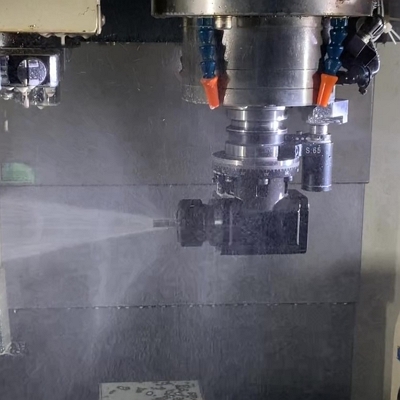
4. PSC Internal and External Tool Post
PSC internal and external tool posts are designed for CNC lathes. After PSC internal and external tool post are installed on the turret, engineers clamp the PSC taper tools on the tool post through PSC interface. Tool change time is reduced by at least 5 times compared to conventional tool post. With coolant pressure up to 130 Bar, PSC internal and external tool posts can help effectively remove chips, extend tool life, and improve the surface finish of workpieces.
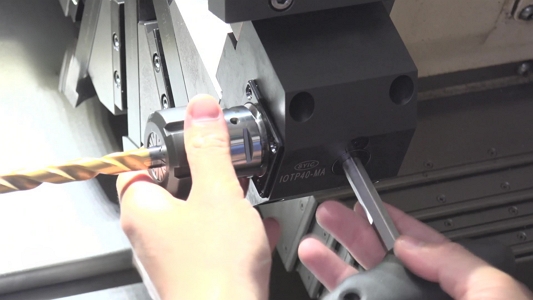
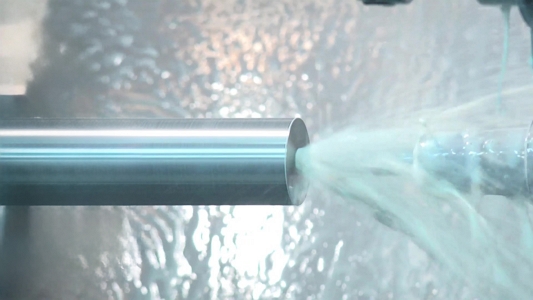
5. BMT Static Tool Holder
SYIC offers a variety of BMT static tool holders suitable for turn-mill machining centers. The jaw clamping design allows for quick tool change. BMT static tool holder utilizes superior repeat positioning accuracy of PSC interface and used with PSC taper tools. These tools can be measured offline in advance, reducing machine downtime. Additionally, they can withstand high coolant pressure up to 70 Bar, providing a superior cooling effect and greatly enhancing machining efficiency.
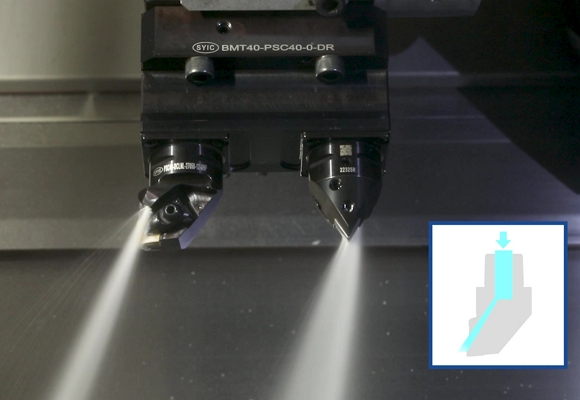
SYIC offers a diverse range of built-in coolant products. Combined with high-pressure coolant systems, they significantly enhance machining efficiency and demonstrate superior machining quality. With continuous advancements in cooling technology, SYIC consistently innovates by launching solutions with various built-in coolant products. We firmly believe that these innovations will continually help our customers push the boundaries of machining and realize the positive impact of advanced machining.
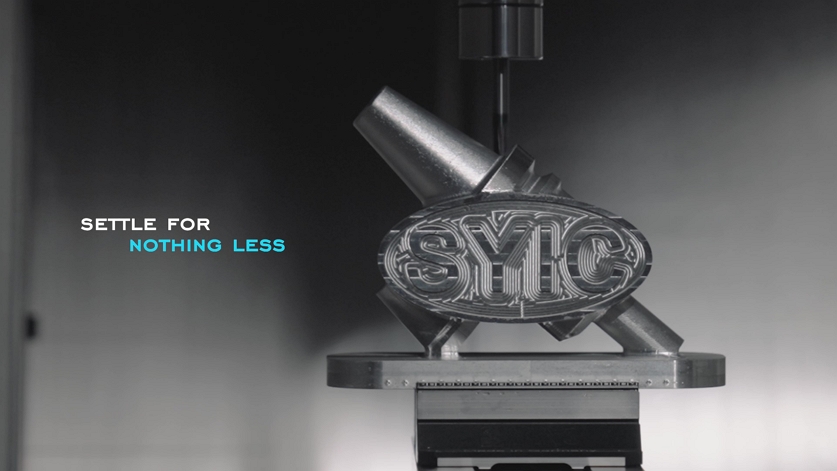