Methods to Improve Production Efficiency
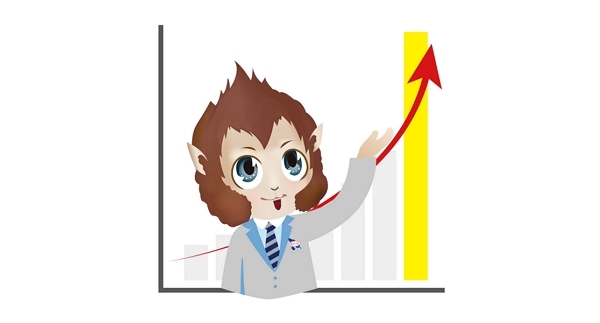
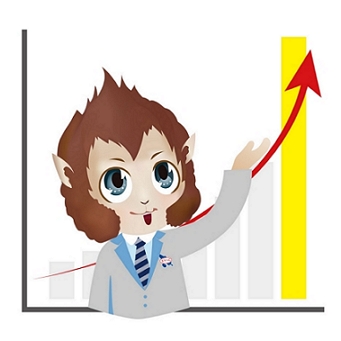
Time is money! How to maximize profits with the same amount of time and resources is a key concern for everyone. Improving efficiency can not only reduce costs, enhance corporate competitiveness, shorten delivery time, and improve employees’ quality of life, but alsocontribute to energy saving and carbon reduction, playing a role in protecting the environment. Let’s explore how to achieve maximum work efficiency in the least amount of time!
Enhancing production efficiency and reducing defect rates are closely tied to the use of good equipment and high-quality tooling accessories. In previous knowledge articles, we shared how choosing the right tool holder can improve efficiency. Beyond that, what other methods can we use to boost efficiency?
- Choosing the Right Equipment: Depending on the shape of the workpiece, determine the necessary machining processes and select the appropriate equipment. This can reduce multiple setups and clamps, save machine setup time, and achieve higher precision and production efficiency.
- Selecting the Proper Tools: Choose tools based on workpiece characteristics, such as material, hardness, and clamping method. This allows you to tailor solutions to specific workpiece properties, increase tool life, reduce tool wear, and save tool procurement costs.
- Setting Optimal Cutting Parameters: The setting of parameters affects product quality and processing time. Setting the most suitable cutting parameters can optimize the machining process, ultimately increasing productivity and machining efficiency.
By applying the above methods, product accuracy and stability can be achieved, leading to improved production efficiency and product quality.
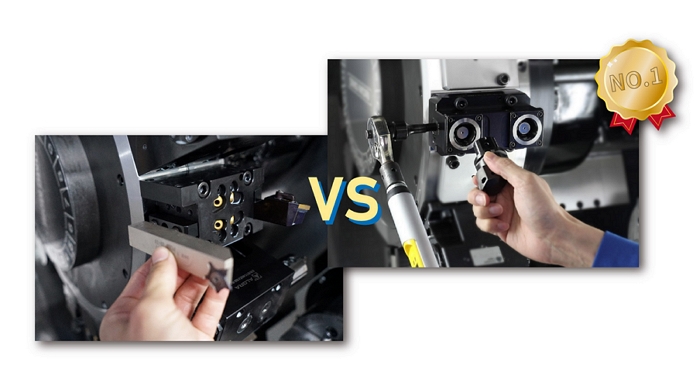
What premium products from SYIC can help improve production efficiency?
In pursuit of a high-efficiency machining environment, SYIC has released the PSC one-piece internal and external tool posts and the BMT static tool holders. These products, designed with a camshaft drive mechanism, enable easy and fast tool changes—requiring only a half-turn to change tools, greatly reducing tool change time and machine downtime. Additionally, both product series are resistant to high coolant pressure, with the former enduring up to 130 bar and the latter up to 70 bar, significantly extending tool life and providing high machining stability and reliability during production.
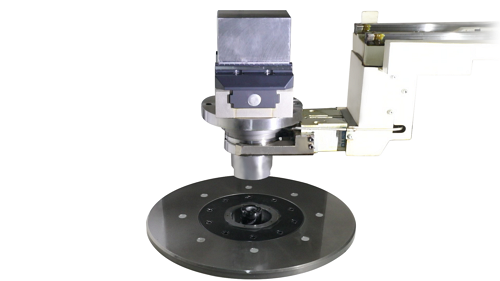
Moreover, SYIC has applied HSK and PSC interfaces in connecting molds, workpieces, and machine tables, launching the AWC jig tool holder, which realizes quick workpiece positioning and clamping. Its multi-sized screw hole design allows direct locking of workpieces and compatibility with various molds.
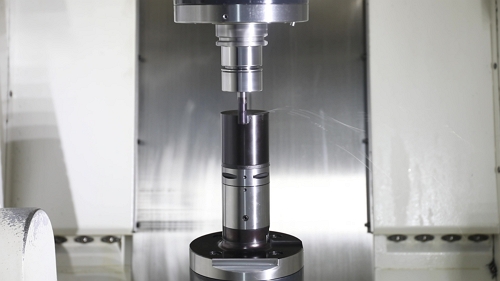
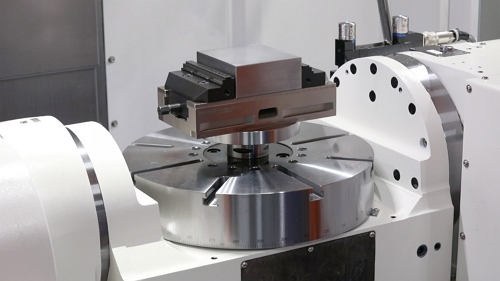
As a leader in tool holder manufacturing, SYIC is committed to helping you solve machining challenges and continues to develop products that boost production efficiency.
This helps you manage time more effectively and achieve a 1+1>2 productivity growth. Let’s work together to create a win-win future!
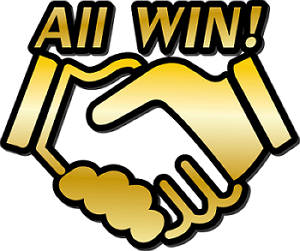